Media Wear Of Steel Balls In Dry Ground Carbonate Roller Mills
.jpg)
A Review of the Grinding Media in Ball Mills for Mineral
2023年10月27日 Chenje et al compared five types of grinding media balls (eutectoid steel, lowalloy steel, mediumchromium cast iron, cast semisteel and unalloyed white cast iron) and 2017年8月29日 More than 95% of the steel grinding components in mills are balls Grinding balls are subject to repeated impacts and also to abrasive wear (in the case of wet grinding in Improving the Quality of Steel Grinding Balls Springer2023年4月23日 One of the most used tumbling mills is the ball mill This paper reviews different types of grinding media that have been developed and improved over the years and their (PDF) Grinding Media in Ball MillsA Review ResearchGate2013年8月1日 In this study, the current understanding of the factors affecting the consumption of steel media in comminution systems in mineral processing are reviewed, together with models Consumption of steel grinding media in mills – A review
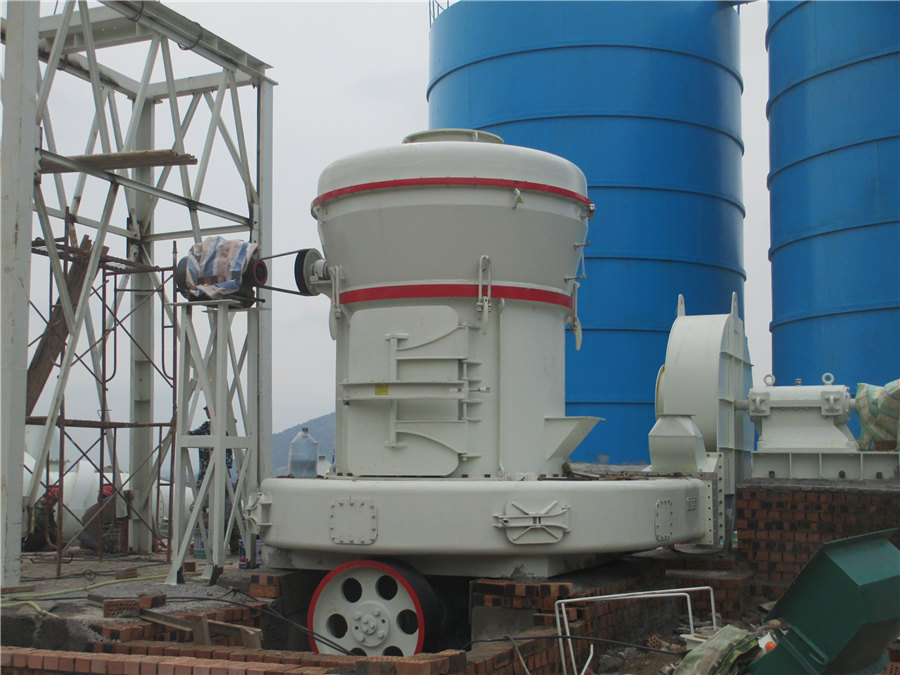
(PDF) A comparison of wear rates of ball mill
2016年1月1日 It gives accurate predictions of the service life of wear resistant alloys in mill liner and grinding media applications In this paper the BMA test methodology was applied to investigate the2020年8月3日 In this study, we investigates the application of three powerful kernelbased supervised learning algorithms to develop a global model of the wear rate of grinding media Modeling and prediction of wear rate of grinding media in 2013年8月1日 In this study, the current understanding of the factors affecting the consumption of steel media in comminution systems in mineral processing are reviewed, together with models Consumption of steel grinding media in mills – A reviewThere are three types of grinding media that are commonly used in ball mills: • steel and other metal balls; • metal cylindrical bodies called cylpebs; • ceramic balls with regular or high Grinding in Ball Mills: Modeling and Process Control
.jpg)
A discussion on the measurement of grinding media wear
2016年7月1日 A survey found out that approximately 53% of the grinding circuits around the world use ball mills, and 38% use autogenous or semiautogenous grinding, and therefore 2022年12月21日 Wear rates of grinding media can be misrepresented by marked ball wear tests (MBWT) Galvanic interactions between dissimilar grinding media can be affected by the Understanding Charge Effects on Marked Ball Wear Rates: a T04:06:49+00:00; Media Lls Composition In Cement Mills parafiamchypl Grinding Media Grinding Balls Union Process, Inc Diameter depending on the material, ranging from 005 mm to 2 mm for small media mills, up to 18 to 1 for traditional Attritors and up to to 2 for ball mills Composition metallic grinding media like carbon steel, forged steel, stainless steel or Live media wear of steel lls in dry ground carbonate mills2013年8月1日 The impact is experienced as the balls cascade under the rotation action of the mill and contact the liners or ore, and this results in the appearance of micro cracks, which enhances wearConsumption of steel grinding media in mills – A review
.jpg)
A Review of the Grinding Media in Ball Mills for Mineral
2023年10月27日 The ball mill is a rotating cylindrical vessel with grinding media inside, which is responsible for breaking the ore particles Grinding media play an important role in the comminution of mineral ores in these mills This work reviews the application of balls in mineral processing as a function of the materials used to manufacture them and the mass loss, as 2019年12月4日 3 Types of Grinding Media for Ball Mills Grinding media, used to extract the concentrate for the production of metals, are the main components in the ball mill grinding process There are different types of milling media used in grinding such as steel balls, ceramic balls and cylpebs Steel balls Steel grinding media are ideal for extracting 3 Types of Grinding Media for Ball Mills FTM MachineryThe ball mill is a tumbling mill that uses steel balls as the grinding media The length of the cylindrical shell is usually 1–15 times the shell diameter (Figure 811)The feed can be dry, with less than 3% moisture to minimize ball coating, or slurry containing 20–40% water by weightBall Mill an overview ScienceDirect Topics2023年10月27日 required for size reduction [1] and determine the category of tumbling mills: autogenous, rod mills and ball mills Autogenous and semiautogenous mills are used in primary grinding whilst rod and ball mills are used in secondary grinding, with the ball mills being the most commonly usedA Review of the Grinding Media in Ball Mills for Mineral
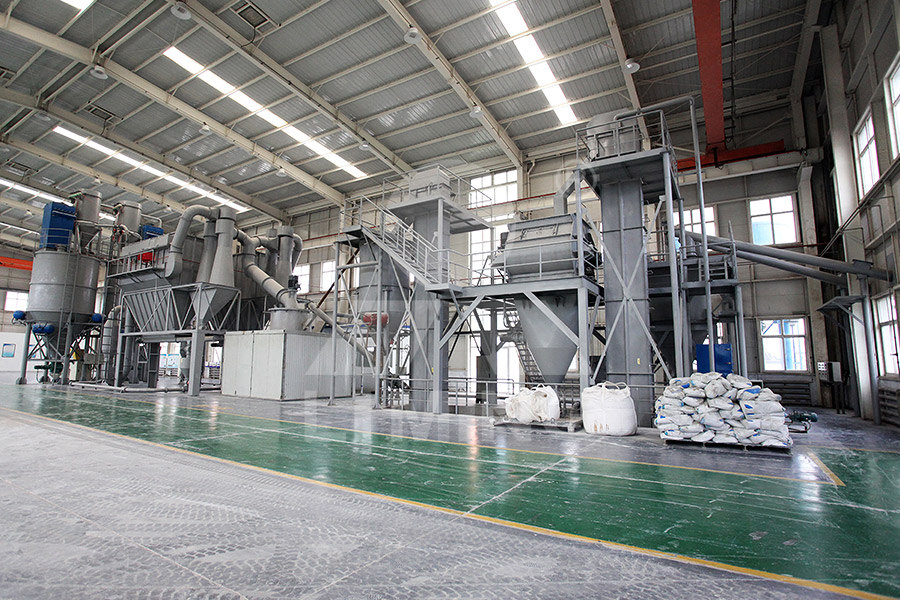
Effective Ball Mill Media for Superior Black Powder Production
2024年8月1日 This is the speed at which the grinding media, such as steel balls, begin to rotate along with the cylindrical device instead of falling and grinding the material Consequently, exceeding the critical speed results in no further grinding Ball mills are essential in the preparation of black powder, with the grinding media playing a crucial role2015年3月1日 Semantic Scholar extracted view of "Effects of rotation speed and media density on particle size distribution and structure of ground calcium carbonate in a planetary ball mill" by Yanru Chen et al Planetary ball mills are able to perform dry and wet grinding Most experimental analyses and computer simulations in this field are mainly Effects of rotation speed and media density on particle size 2013年8月1日 Comminution accounts for an estimated 30–50% of typical mining operating costs, and of these, liner wear and media consumption account for roughly 50% of the cost According to Moema et al (2009), in some instances, media wear can constitute up to 40–45% of the total cost of comminutionConsumption of steel grinding media in mills – A review2024年10月16日 Rare Earth stabilized Zirconium oxide Grinding Media (spgr 58 to 61) ZrO2 + CeO Yellow or black, very hard Sizes from 400 microns to 2″ Medium cost Yttrium stabilized Zirconium oxide Grinding Media (spgr 60) 95% ZrO2 + 5% Y2O3 Best wear properties of all grinding media, very round and very smooth, narrow size spreadsLargest selection of grinding media Glen Mills, Inc
.jpg)
Guide to Calcium Carbonate Grinding: Mills,
2023年6月25日 The ball mill can be operated either wet or dry The particle size of the finished product can be adjusted by controlling the grinding time, rotating speed, size and composition of grinding media, additives, etc Typically, ball Applications of ball mills and agitated media mills Ball mills have been used to produce highquality mineral flours for many years They are suitable for grinding mediumhard to extremely hard, brittle and fibrous materialsSpecific applications include industrial minerals, metal oxides, glass, graphite, limestone, quartz, zircon sand, talc, ceramic paints, inorganic pigments, Ball Mills Agitated Media MillsApplications of ball mills and agitated media mills Ball mills have been used to produce highquality mineral flours for many years They are suitable for grinding mediumhard to extremely hard, brittle and fibrous materialsSpecific Ball Mills Agitated Media Mills Hosokawa 2024年1月26日 Axial rotation of ball mill provides cascading action of steel balls which crush the raw material due to attrition between steel balls which is known as grinding media Grinding media is mostly prepared from high chrome steel Ball mills are efficiently utilized for final grinding of clinker It grounds the raw mix (clinker) into fine putation of charging media for a double compartment cement ball
.jpg)
Grinding Media in Ball Mills for Mineral Processing
2023年11月24日 The ball mills are either used in a drymilling or wetmilling setup depending on the needs of the industry in which they are utilised The cement and pharmaceutical industries normally use dry grinding whereas the mineral processing industry mostly resorts to wetmilling The grinding media, such as steel balls, generate a breakage force 1998年5月15日 Factors such as the cushioning effect of the ground powder on grinding media smaller than a certain size, particularly in dry grinding, have to be recognized 92 hu:reasing the mill aT)eed Herein lies the advantage of increasing the mill speed, which in effect increases l:he collision velocity and the number of collisions per unit time Energetics of collision between grinding media in ball mills 2024年6月29日 Grinding media influence the energy consumption and efficiency of the grinding process during the calculation of the Bond Work index (BWi), a wellknown method for selecting comminution equipment, evaluating milling efficiency, and calculating required milling power Traditional grinding tests often choose steel balls as the grinding media, but ceramic balls are A New Approach to the Calculation of Bond Work Index with Media Wear Of Steel Balls In Dry Ground Carbonate Ball Mills Media Wear Of Steel Balls In Dry Ground Carbonate Ball Mills Grinding Ballgrinding Rodforged Steel Grinding Ballcast, Cast steel grinding balls are made by highquality raw materials the good casting process ensures the compactness and broken rate of the steel balls and can be well applied in ball mills with media wear of steel balls in dry ground carbonate ball mills
.jpg)
Grinding Media, Grinding Balls NETZSCH Grinding
3 天之前 The grinding media, also referred to as grinding balls or grinding beads, serve as the tools in mills with freely moving grinding media, such as agitator ball mills The movement of these grinding balls within the mill generates various stresses between the balls and the product, including impact, pressure, friction, and shearPlanetary ball mills are ideal for nanoscale grinding and mixing Vibratory Ball Mills: Utilizing vibrations, these mills are suitable for ultrafine grinding and mixing of materials Vibratory ball mills provide highenergy input to the grinding media, resulting in Ball Mill Grinding Machines: Working Principle, Types, Parts 2022年1月1日 Experiments reported by Malghan [29] for different sizes of ball mills were analysed to obtain the grinding rate of calcium carbonate as ground material and steel balls as grinding media Cumulative particle size distribution curve was plotted and used to obtain the particle size for 50% cumulative passing level for a given time which was known Impact energy of particles in ball mills based on DEM simulations Chenje et al [21] compared five types of grinding media balls (eutectoid steel, lowalloy steel, mediumchromium cast iron, cast semisteel and unalloyed white cast iron) and found that heattreated medium chromium (HTMC) cast iron balls had superior qualities in terms of microstructure and wear resistance despite, their high cost per ton(PDF) A Review of the Grinding Media in Ball Mills for
.jpg)
(PDF) Effects of Ball Size Distribution and Mill Speed and
2020年7月2日 A comprehensive investigation was conducted to delineate the effect of ball size distribution, mill speed, and their interactions on power draw, charge motion, and balls segregation in a However, the unit cost for wear parts for a ball mill is much lower than for a vertical roller mill For a ball mill grinding OPC to a fineness of 3200 to 3600 cm2/g (Blaine) the cost of wear parts (ball, liners and mill internals) is typically 015020 EUR per ton of cementCement grinding Vertical roller mills VS ball mills2024年5月27日 Ball mills’ efficiency and performance can be optimised through proper design, maintenance, and advanced technologies like MechProTech’s TITAN Ball Mill and TITAN Automatic Ball Charger Investing in cuttingedge equipment improves operational efficiency and contributes to a more sustainable and productive future for the mineral processing Ball Mills in the Mineral Processing Industry MechProTech2014年12月24日 Recently, Chen et al (2015) studied the effects of rotational speed and media density on particle size distribution and structure of ground calcium carbonate using a planetary ball mill A Effects of rotation speed and media density on particle size
.jpg)
Morphology and wear of high chromium and austempered ductile iron balls
2021年11月1日 High chromium balls are recognized as better grinding media in terms of wear rates than forged steel balls, which are conventional grinding media in the milling process of iron ore2020年7月1日 Considerable investments have been made on the development of alternative equipment It is reported that the use of stirred media mills and high pressure grinding rolls (HPGR) improved grinding efficiencies compared to the conventional tumbling mills – balls mills and rod mills [11], [30], [31]The development of new approaches to mineral processing, such A critical review on the mechanisms of chemical additives Applications of ball mills and agitated media mills Ball mills have been used to produce highquality mineral flours for many years They are suitable for grinding mediumhard to extremely hard, brittle and fibrous materialsSpecific applications include industrial minerals, metal oxides, glass, graphite, limestone, quartz, zircon sand, talc, ceramic paints, inorganic pigments, Ball Mills Agitated Media Mills Hosokawa AlpineApplications of ball mills and agitated media mills Ball mills have been used to produce highquality mineral flours for many years They are suitable for grinding mediumhard to extremely hard, brittle and fibrous materialsSpecific applications include industrial minerals, metal oxides, glass, graphite, limestone, quartz, zircon sand, talc, ceramic paints, inorganic pigments, Ball Mills Agitated Media Mills Hosokawa Alpine
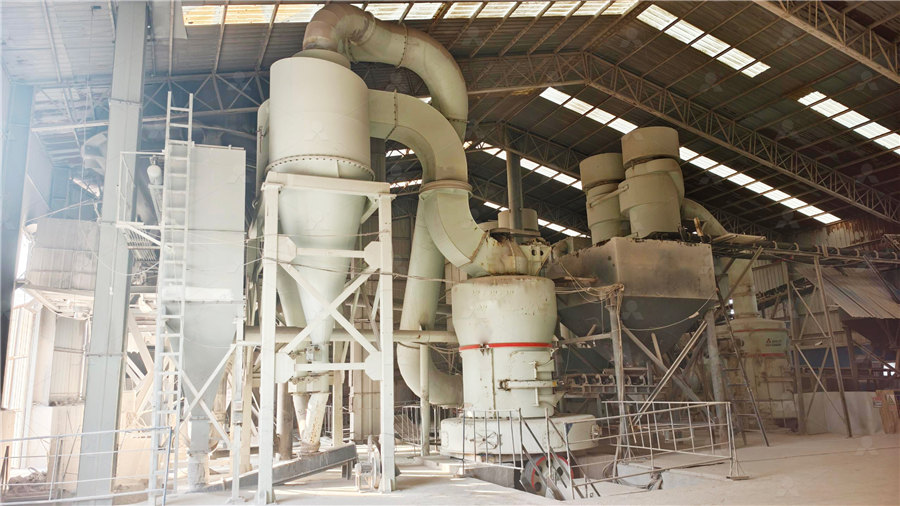
Ceramic ball wear prediction in tumbling mills as a grinding media
2014年12月1日 1 Introduction The kinetics of grinding media wear is estimated based on theories put forward shortly before the second half of the Twentieth Century, as is evidenced in the work of Sepúlveda [1], which uses the theory of linear wear to calculate specific rate constant wearOther research approaches were found such as that of Albertin and Sinatora [2], in which 2017年8月29日 65% of the total costs [1] More than 95% of the steel grinding components in mills are balls Grinding balls are subject to repeated impacts and also to abrasive wear (in the case of wet grinding in aggressive oxidative media) Accordingly, they must be shatterresistant (stable under impact); and resistant to wear and corrosion [1–4]Improving the Quality of Steel Grinding Balls Springer2024年7月12日 Some of the most common types include tumbling ball mills, planetary ball mills, and vibratory ball mills A conical ball mill, known for its efficiency in grinding, operates with changes in ball size and kinetic energy as the discharge outlet is approached While they may differ in design and operation, all of these ball mills share the same What Is a Ball Mill and How Does It Work? (Overview 2024)2020年10月8日 Friction and wear are the primary factors for the failure of liners, which affects the lifting capacity and milling cost in ball mills However, there are no effective methods to measure and Experimental Study on Multibody Friction and Wear
.jpg)
Wear ofgrinding media in the mineral processing
2018年11月9日 SAG mills and calculated the wear rate exponent to be 28 This implies that SAG balls wear fastest at their full size and wear progressively slower as their mass is decreased Accepting a wear exponent of 28 for SAG mills is valid when describingthe ball's wear when the ball isstillrelatively large [>75mm (3 in)] However, a wear rate 2024年2月19日 The quality of the steel balls determines the amount of ore added per ton They are using new wearresistant steel balls Good quality steel balls are added based on the amount of ore processed per ton (that is, 08kg per ton of ore) Generally, steel balls are required to process one ton of ore (1kg12kg)Ball Mill Steel Balls: Quality And Gradation JXSC Mineral1999年11月1日 Dry comminution processes with jet mills or roller mills are hardly suitable for the comminution of these materials to submicron sizes and also comminution in ball mills has its limits Thus, stirred media mills are increasingly used for the comminution of ceramics They show a higher power density than ball mills, and are generally more Comminution of ceramics in stirred media mills and wear of Premium carbon steel grinding balls for ball mills Durable, consistent costeffective carbon steel milling media for industrial operations these steel balls are the perfect grinding media for your ball mill when chrome is not an option due to your formulation’s composition or contamination Each carbon ball is meticulously engineered Carbon Steel Balls Carbon Steel Grinding Media Milling Media
.jpg)
A Comparative Analysis: Vertical Roller Mill vs Ball Mill
2023年9月21日 The material is fed between the rollers and is crushed or ground as it passes through the gap between the rollers Roller mills are generally larger in size compared to ball mills Grinding Efficiency Ball Mill: Ball mill is known for their high grinding efficiency The grinding media (balls) have a larger surface area and impact the material