Raw Mill And Cement Mill For Cement Production Process
.jpg)
The Cement Plant Operations Handbook International
2019年4月30日 The Cement Plant Operations Handbook is a concise, practical guide to cement manufacturing and is the standard reference used by plant operations personnel worldwide Providing a comprehensive guide to the entire cement production process from raw material2021年7月5日 The cement raw mill is the primary piece of equipment used in the modern cement industry for the raw meal production process As a result, it is critical to investigate the exergy efficiency in a cement raw mill in order to Full article: Evaluation of optimization Raw mill is generally called cement raw mill, raw mill in cement plant, it refers to a common type of cement equipment in the cement plant In the cement manufacturing process, raw mill in cement plant grind cement raw materials Raw Mill, Cement Raw Mill, Raw Mill In Cement 2019年10月23日 together in a raw mill to a particle size of 90 micrometres, producing “kiln feed” Cement Plant: The Manufacturing Process worldcementassociation 1 Limestone (CaCO3) Cement Plant: The Manufacturing Process 4 5 World
.jpg)
Process characteristics of clinker and cement production
2018年11月30日 New ratebased model was developed and used to validate fullscale CAP simulations for cement plants Upcoming work: CAP optimization CEMCAP framework 2024年5月22日 The raw materials, now known as kiln feed, enter a raw mill that consists of a drying chamber and a grinding chamber The kiln feed is then fed into a rotary kiln, a large A practical guide to improving cement manufacturing 2018年1月1日 In this chapter, methods to determine the magnitudes and causes of the exergy destruction rate for the raw mill process in the cement industry were investigated in detail Thermodynamic Performance Analysis of a Raw Mill System in a Cement From the production experience of many cement plants, the selection of cement equipment, especially raw mill, will directly affect the project investment, production schedule and economic benefits At present, in order to adapt to Raw Mill – Raw Mill In Cement Plant AGICO
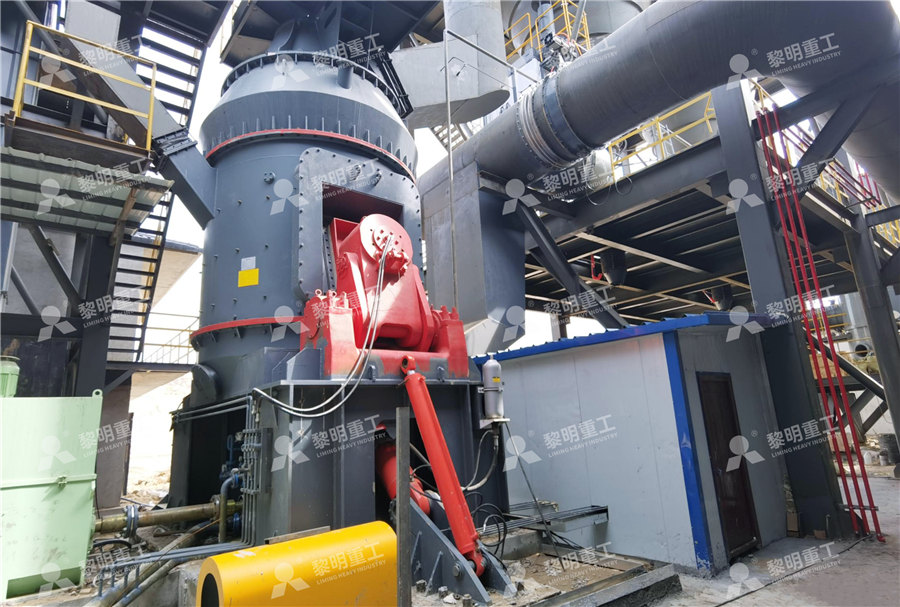
Energy and exergy analyses of a raw mill in a cement production
2006年12月1日 The aim of this study was to determine energy and exergy utilization efficiencies for a raw mill in a cement production Mass balance and heat losses, energy and exergy Cement mills are critical components in the cement manufacturing process, responsible for grinding raw materials into fine powder to produce cement Optimizing the operation of cement mills is essential to maximize productivity, Cement Mill Optimization: Practical Strategies 2014年6月10日 Cement manufacturing process Download as a PDF or view online for free (Fe) • Typical Raw Materials: – Limestone (CaCO3) – Sand (SiO2) – Shale, Clay (SiO2, Al2O3, Fe2O3) – Iron Ore/Mill Scale (Fe2O3) Cement manufacturing process PPT Free 2023年8月23日 A cement mill is a fundamental component of the cement manufacturing process, playing a vital role in breaking down and grinding cement clinker into fine powder This finely ground powder, when mixed with other What Are the Parts of a Cement Mills? Cement
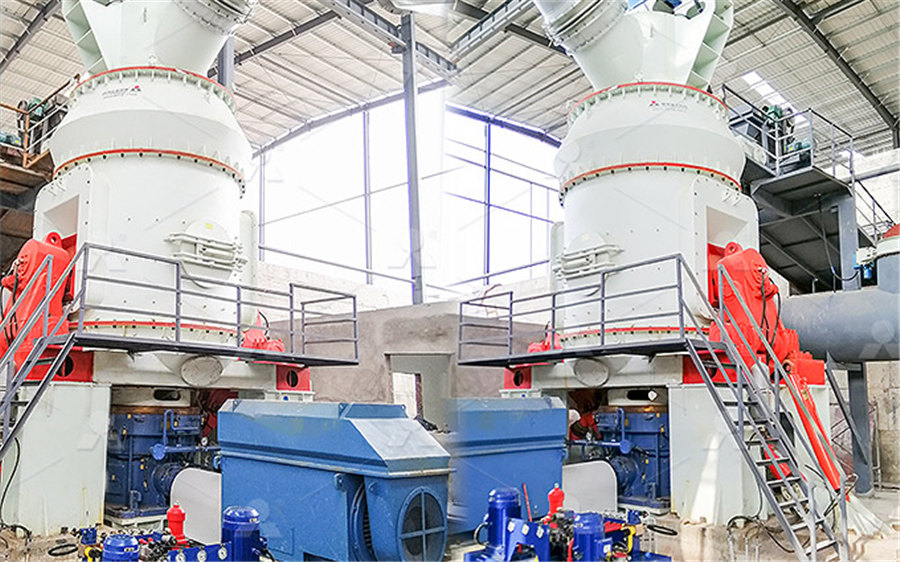
The Cement Plant Operations Handbook International
2019年4月30日 Providing a comprehensive guide to the entire cement production process from raw material extraction to the finished product, the industry’s favourite technical reference book is now fully Finish mill – 12 Cement – 13 Quality control – 14 Packing and distribution – 15 Emission abatement (dust, NO x, SO 2, etc) – 16 2023年8月17日 across different mill sizes for cement and raw applications OK™ raw OK™ cement Example of 4 and 6roller OK™ mills with common parts Sharing of common parts The sharing of common parts is not limited to raw and cement mills of the same size but also extends across different mill sizesOK™ mill The most reliable and efficient mill for raw and 2024年9月5日 These raw materials are blended in definite quantities to obtain a uniform and homogeneous raw mix which is very crucial in the production of good quality cement The Manufacturing Process of Cement Now, let’s explore the steps involved in the cement production process in more detail: 1 Mining and CrushingA Comprehensive Guide to the Cement Manufacturing Process2020年1月27日 Before starting an excellent cement plant, it is necessary for a new beginner to learn cement manufacturing process first So AGICO CEMENT who has plenty of experience in supplying cement plant and cement equipment will give you a full guide on cement manufacturing process From now on, the most energy consumed by the raw mill is converted Cement Manufacturing Process: 6 StepsTo Make Cement Cement
.jpg)
Cement Manufacturing Process and Its Environmental Impact
2023年7月10日 The cement manufacturing process involves the extraction and processing of raw materials, such as limestone, clay, and shale, which are then heated in a kiln at high temperatures to form clinker2020年8月25日 How much do you know about cement production process? A full cement production process includes the cement crushing process, raw mill process, clinker process, and cement grinding process, cement packing process, and related process Find more! Skip to content +86 s aboutCement Production Process Cement Manufacturing Process AGICO CEMENT2015年8月1日 The aim of this article is to improve the management of resources used in the cement production process and mitigate their environmental effects The material efficiency values for a raw mill Analysis of material flow and consumption in cement production processThe vertical roller mill (VRM) is a type of grinding machine for raw material processing and cement grinding in the cement manufacturing processIn recent years, the VRM cement mill has been equipped in more and more cement Vertical Roller Mill Operation in Cement Plant
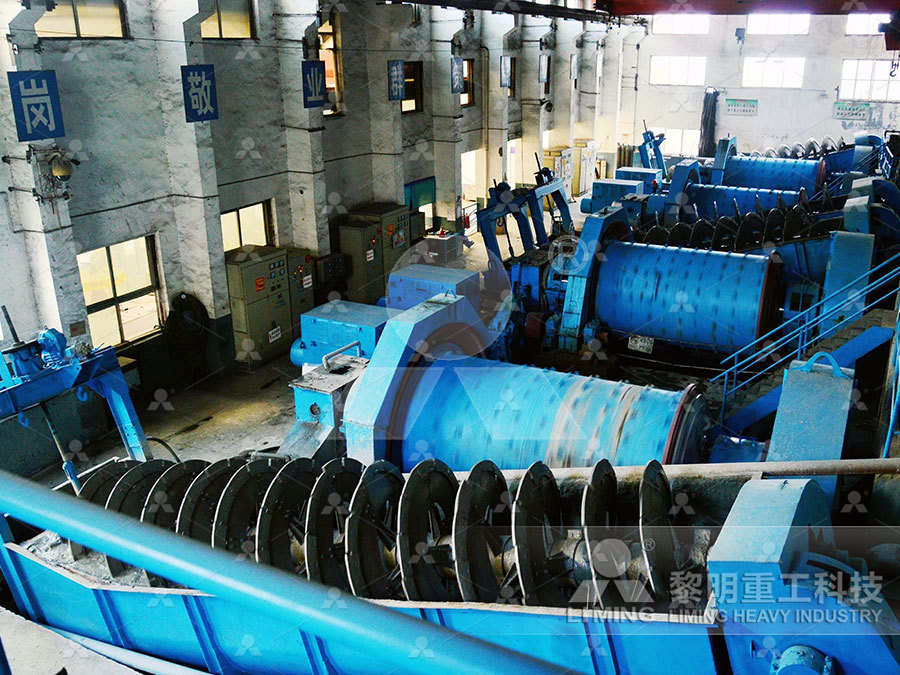
Preparation Of Cement Raw Material Cement
Grinding: grinding all materials into required fineness by cement mill Cement ball mill and vertical cement mill are two common types Homogenizing: homogeneous kiln feed is the precondition of clinker production, so 2021年7月5日 The cement raw mill is the primary piece of equipment used in the modern cement industry for the raw meal production process As a result, it is critical to investigate the exergy efficiency in a cement raw mill in order to Full article: Evaluation of optimization 2019年10月23日 The cement is then packed and distributed to consumers The kiln feed is blasted in a cement kiln at a temperature of 1450oC, causing clinkering to occur (small balls of up to 25mm diameter) 6 5 Raw mill Preheated tower Cement storage silos Packing warehouse Raw material silos Limestone storage and preblending unit Rotary Kiln Additives Silos Cement Plant: The Manufacturing Process 4 5 World Raw mill is the grinding equipment applied in the raw material preparation processIn the wet process of cement production, raw materials should be ground into raw slurry with a water content of 30% – 40% While in the dry process of cement production, they will be ground into dry powder in a cement raw millCement Mill Cement Grinding Machine AGICO Cement Grinding Mill
.jpg)
Raw Mill in Cement Plant Cement Manufacturing Raw
2 天之前 Learn about the raw mill in cement plants and the basic raw materials used in cement manufacturing Discover our efficient cement manufacturing process Contact us for more info! Amrit Support About Amrit Support; Services; Activities; Corporate Annual Return FY 202021; FY 202122; FY 202223;Raw mill is also called cement raw mill, similar to cement ball mill, it is an important cement milling equipment used in the cement production process Raw mill is mainly used for grinding cement raw meal in the cement factory production process It is also suitable for metallurgical, chemical, electric power and other industrial mining enterprises to grind various ores and other grindable Cement Raw Mill in Cement Plant for Cement Raw Meal 1 天前 The desired raw mix of crushed raw material and the additional components required for the type of cement, eg silica sand and iron ore, is prepared using metering devices Roller grinding mills and ball mills grind the mixture to a fine powder at the same time as drying it, before it is conveyed to the raw meal silos for further homogenisationHow Cement Is Made Heidelberg Materials2016年1月20日 In the surveyed cement plant, three balances are established between input and output material in the raw mill, clinker production, and cement grinding system 248 t, 469 t, and 341 t of materials are required to produce a ton of the product in raw material preparation, clinker production, and cement grinding stages; waste gases account for Analysis of material flow and consumption in cement production process
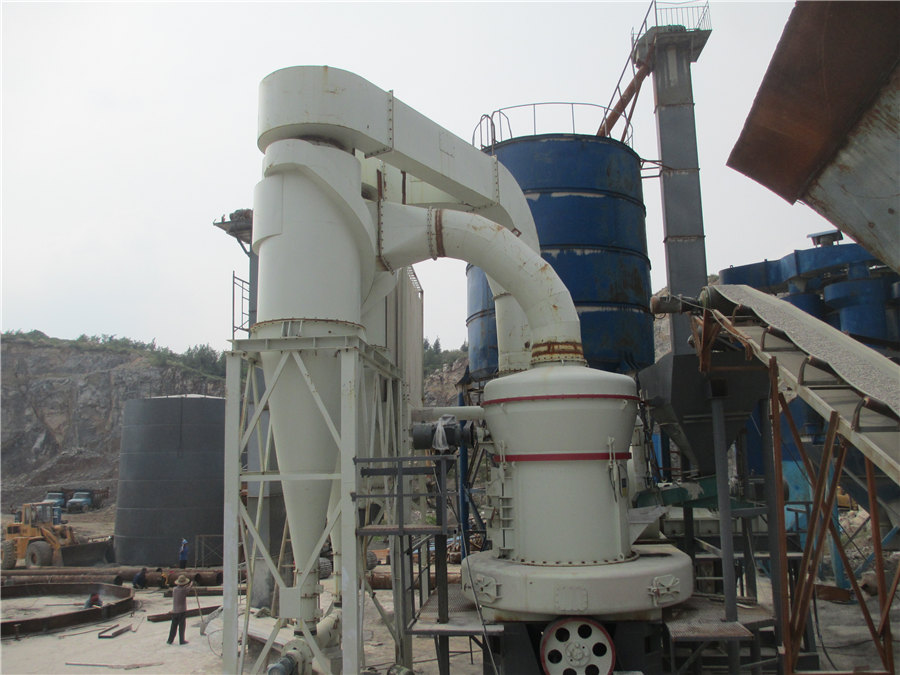
Cement Manufacturing Process INFINITY FOR CEMENT EQUIPMENT
The principal raw materials for cement manufacturing are: Limestone; Silica and alumina from basalt , shale or sand; Iron from iron ore or steel mill scale Sand stone; Pumice (volcanic ash for Portland Pozzolana cement ) Gypsum General Properties of Raw Material Sources Limestone; The basic raw material of the cement production is limestoneAfter being crushed by the raw mill, the raw meal is ready to enter the preheater The cyclone preheater is one of the core equipment for dry process cement production, which consists of a series of vertical cyclones locate on several How Is Cement Produced in Cement Plants2023年11月1日 The design of the raw material grinding system should focus on the energysaving, vertical mill grinding system because of its powersaving, simple process to become a large cement plant, the use of a ball mill grinding 8 Tips For Cement Plant Design Cement 2022年7月4日 Figure 28: Showing the raw mill at stationary, Shayona cement factory The raw mill has capac ity of 50 tons per hour and takes 300KW of electricity The mill’s mainMining Activities, Cement Production Process

Cement Analysis and Production Information Thermo
While the cement production process before the kiln is focused on the elemental makeup and proportions of the raw materials, after the clinker is produced, the focus shifts to the molecules these elements form As an example, Iron (Fe) is present in the raw mix and is required in a certain proportion in the raw mix, but the same iron in Vertical raw mill is one kind of raw mill, generally used to grind bulk, granular, and powder raw materials into required cement raw meal in the cement manufacturing plantVertical raw mill is an ideal grinding mill that crushing, drying, grinding, grading transfer set in one It can be widely used in cement, electric power, metallurgy, chemical industry, nonmetallic ore, and other industriesVertical Raw Mill Cement Raw Mill Raw Mill In Cement Plant2024年3月7日 The cement manufacturing process involves the extraction and processing of raw materials, such as limestone, clay, and shale, which are then heated in a kiln at high temperatures to form clinkerCement Manufacturing Process and Its Environmental 2022年5月9日 Cement production is one of the most energyintensive manufacturing industries, and the milling circuit of cement plants consumes around 4% of a year's global electrical energy production It is Modeling of energy consumption factors for an industrial cement
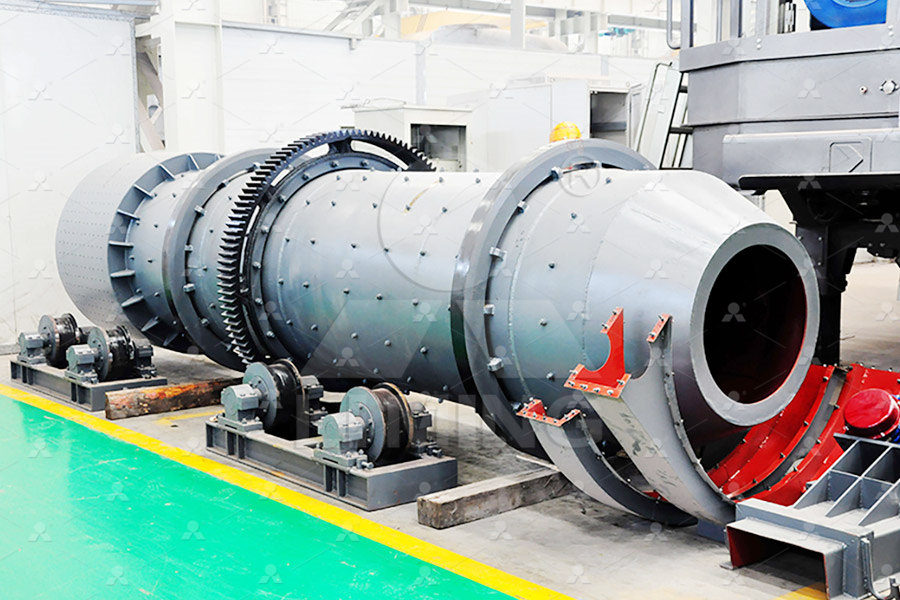
Chapter 4 Cement Manufacturing and Process Control
2019年8月26日 Cement Manufacturing and Process Control 41 Cement Manufacturing: Basic Process and Operation To design the Refractory for the lining of different equipments in a cement plant, it is necessary to understand the total operational process of a cement plant in depth It is necessary to know the conditions prevailing in different equipments and the2018年11月30日 Cement production process: Thermal energy demand and CO 2 emissions 30% fuel emissions thermal energy prod process emissions from calcination of limestone 60% 10% electric power consumption, indirect emissions Limestone Quarry Filter Clinker Cement Cement Mills Raw Mill Calcination Cement Constituents Crusher FanDrying Rotary Kiln Process characteristics of clinker and cement production2023年12月20日 In this process, the chemical bonds of the raw materials are broken down and then they are recombined into new compounds The result is called clinker, which are rounded nodules between 1mm and 25mm across The clinker is ground to a fine powder in a cement mill and mixed with gypsum to create cementThe Cement Manufacturing Process Thermo Fisher ScientificIn this article, we will look at the cement manufacturing process, its applications, some types of cement and cement testing Jump to Section Applications of the Different Types of Cement; Horizontal mills, similar to those used to grind Cement: Applications, Manufacturing Process,
.jpg)
Cement Manufacturing—Technology, Practice, and
2021年11月16日 76 4 Cement Manufacturing—Technology, Practice, and Development Fig 42 Modern dry process cement production process 424 Manufacturing of Cement Clinker The prepared raw material is called the “kiln feed” and is fed to the kiln In the kiln, this kiln feed is subjected to a thermal treatment process which consists of2015年1月1日 Vertical cement mill (vertical mill) is a machine that plays an important role in the raw meal production process of the newtype dry cement, and it is a set breakage, drying, grinding, transport in one []Raw material grinding process is a vital and energy consumption link in the cement productionModeling Based on the Extreme Learning Machine for Raw Cement Mill In another word, the cement grinding mill can increase the cement quality and guarantee the qualification rate of cement In general, cement mill can both apply for dry cement production and wet cement production Commonly, there are three hot types of cement mill in the cement industry: cement ball mill, Raymond mill, and vertical cement mill Cement Mill Cement Ball Mill Vertical Cement Mill Cement 2024年3月16日 The cement manufacturing process involves 6 key phases: 1) Raw material extraction through quarrying, 2) Grinding, proportioning, and blending of raw materials, 3) Preheating of materials using hot gases from the kiln, 4) Firing materials in a rotating kiln at 1450°C to form clinker, 5) Cooling of clinker using forced air, 6) Final grinding of clinker along with Cement Manufacturing Process PDF Mill (Grinding) Scribd
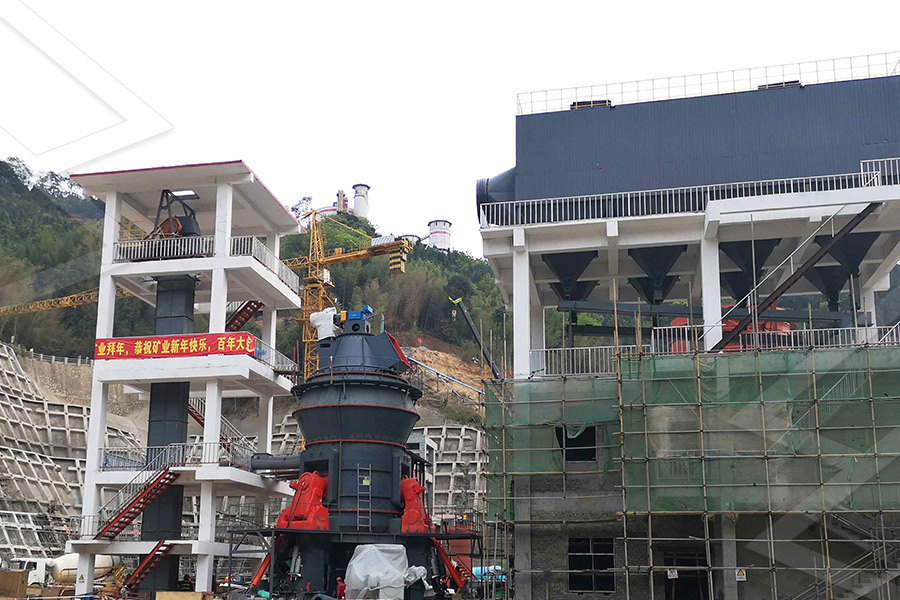
Raw Mill and Kiln Feed Consistency: Key to Efficient Cement Production
This process involves blending raw materials to create a uniform mix before feeding it into the raw mill Modern blending systems use stacking and reclaiming methods like chevron stacking, windrow stacking, and circular blending beds to achieve uniformity in feed composition Consistency in Cement Production: Strategies for Raw Mill and Although the mill was originally designated for cement production, the flexible layout allowed the grinding tests to be carried out for raw materials and coal as well In an industrially operating Horomill, grinding takes place in a rotating shell (say, 3800 mm diameter in a given instance) at a rotation speed of 38 rpm actuated by a 2500 kW Everything you need to know about cement Materials Preparation and Raw 2024年8月20日 Step 4: Cement grinding and storageThe cooled clinker with gypsum is finely ground in a cement mill to form the hard cement The other raw materials are added during the grinding process The raw material added during the grinding process defines the quality of the cement Therefore, the raw materials determine the cement gradeUnderstanding the Raw Materials for Manufacturing Cement2023年5月27日 cement raw mill is the primary piece of equipment used in the modern cement industry for the raw meal production process As a result, it is critical to investigate the exergy efficiency in a cement raw mill in order to satisfy the need for the design and optimization of the cement plant manufacturing processEvaluation of optimization techniques for predicting
.jpg)
From raw materials to cement
2022年2月12日 with the extraction of raw materials and ending with the finished product From raw materials to cement Extracting raw materials Crushing and transportation Raw material preparation I: Storage and homogenisation Raw material preparation II: Drying and raw grinding Burning The burning of the raw meal at approx 1,450°C is carried out